
2014 International Aluminum Extrusion Design Competition
Professional Class Winning Entries
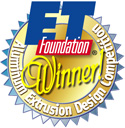
A total of $7,500 was awarded to the winning designers in the Professional Class for the 2014 Aluminum Extrusion Design Competition. There were no winning entries in the Alternative Energy and Structural Categories this year. Therefore, $4,000 in award money from these two categories was transferred to the Student Class.
Grand Prize: "Hercules" Patient Repositioner by David Hornbach of The Morel Company
Engineered Products: LED heat sink assembly by Richard Hinkle and Joe Becknell of Magnode Corporation
Transportation: the "Kargo" light utility vehicle by Stephan La Chevrotiere from Service Precicad Inc
Honorable Mention: retrofit parking sign by Stephan La Chevrotiere of Service Precicad Inc
Cash awards and scholarships for the 2014 Aluminum Extrusion Design Competition sponsored by Sapa Extrusions North America
*Click on the thumbnail of each image to be taken to the larger, higher-resolution image*
Grand Prize:"Hercules" Patient Repositioner by David Hornbach, Senior Product Designer for The Morel Company in Batesville, Indiana
David Hornbach, Senior Product Designer for The Morel Company in Batesville, Indiana, won the Grand Prize earning him the top prize of $3,500 for his design of the "Hercules" Patient Repositioner. The Hercules allows a single caregiver to reposition a patient in bed with a simple push of a button. "Every day, hospital caregivers struggle with pulling patients up in the bed, putting their bodies at risk for injury," noted Hornbach in his Design Competition entry. For patients, the process is uncomfortable and unsafe, and for administrators, traditional repositioning causes patient inefficiencies, lost work days, and more, according to the designer.
The repositioner uses a special sheet that rolls into the aluminum housing, pulling the patient back up to the top of the bed. The unit is comprised of 7 unique aluminum extrusions that include two cavities, one that houses a roller that repositions the sheet, and one that houses the motor, clutch, circuitry, and power supply. Hornbach notes of the motor housing side of the unit, "This cavity was designed for easy service and creating a closure which could withstand our fluid ingress, EMC and grounding requirements."
Hornbach cited many of extruded aluminum's advantages as reasons why the material was chosen for the Hercules. "Creating a chassis that can handle the 600 in/lbs. of torque and still be small enough to fit under a cutout in the mattress made aluminum the natural choice." Other advantages included extruded aluminum's recyclability, strength-to-weight ratio, low tool cost, reduced parts, and more.
Explaining the creative geometry that the extrusion design process affords, Hornbach noted, "The external shapes of some of the components (mainly the waterfall edge) are precise and are integral to the efficiency of the system. This geometry would be difficult to produce with other processes."
In addition, using extrusions for this design saved the company money. "The flexibility in the process allowed us to purchase a majority of our parts from one vendor," said Hornbach. "In fact, we are investigating turning more pieces into extrusions."
Hornbach also praised the extrusion industry for their help. "The aluminum extrusion community has done a terrific job making design data accessible for engineers. All tolerances and expectations were known before even meeting with a vendor. This took the 'black art' out of the design process and helped the Morel engineers have the initial designs manufacturing ready."
"The use of aluminum extrusions allowed us here at the Morel Company to bring [this product] to market quickly with low overhead and the lowest part total possible," said the designer.
Competition judge Joseph Benedyk, Editor of Light Metal Age magazine and Research Professor at Illinois Institute of Technology in Chicago, said of the design, "This entry is truly an engineered product made of multiple extruded components engineered to work together to solve a real world problem in the medical field. It's a great example of how extrusions can save time and money."
![]() |
![]() |
Engineered Products: LED heat sink assembly by Richard Hinkle and Joe Becknell of Magnode Corporation
Richard Hinkle, Vice President of Sales & Marketing, and Joe Becknell, Sales Engineer, of Magnode Corporation in Trenton, Ohio, won First Place in the Engineered Products Category for an LED heat sink assembly for hazardous industrial lighting. The assembly is made of one extruded profile hub and 36 profile fins. The entire assembly weighs less than 30 pounds and is 15 inches in diameter. In order to meet tight tolerance, anodizing, machining and post assembly specifications, the heat sink could not be extruded as a single profile. Advantages of using aluminum extrusion for this application included high strength-to-weight ratio and zero porosity versus a casting design. In addition, the ability of extruded aluminum to be precision cut, easily deburred, sub assembled, anodized, CNC machined, cleaned and packed with screw sets, enabled the company to achieve reduced lead times and lower tooling costs.
"The heat sink assembly provides safe, reliable heat transfer characteristics, simple installation and replacement, custom optics, and high efficiency and lumen output," explained Hinkle and Becknell in their entry.
![]() |
Transportation: the "Kargo" light utility vehicle by Stephan La Chevrotiere from Service Precicad Inc
Stephan La Chevrotiere, an industrial designer at Service Precicad Inc in Quebec, Canada won first place in the Transportation Category for his design of the an electric utility vehicle for industrial use. The cab of the "Kargo" light utility vehicle was designed using aluminum extrusions to replace aluminum sheet and welded tubing. The Kargo, which is already in production, is used in the aluminum smelting industry. Although the use of aluminum in the design of such vehicles is not common, explained La Chevrotiere, "working in the aluminum business and the fact that the vehicle is 100% electric were two factors that led us to this choice [of using extruded aluminum for the design]."
The designer pointed out several factors where designing the vehicle with extrusions clearly showed a cost benefit over the original design, which he noted was too high for mass production. In evaluating the original sheet and tube design for improvement, the biggest flaws were identified, including a great deal of outsourcing for fabrication, high cost for cabin preparation and painting, high transportation costs and difficulty in customizing the vehicle for various workloads. Following "several design reviews, we came up with the idea of designing our own extrusions that would integrate the features we normally had welded onto our structure," explained the designer. Using extrusions, Precicad was able to eliminate at least 80-percent of the welding on the cabin frame, and instead assembled the cabin with structural rivets. The extrusions are pre-painted and delivered directly to Kargo facilities, cut to length and the final fabrication is then accomplished in-house. La Chevrotiere said that the cost for fabrication of the cabin was reduced from $4,200 to $3,000 with the revised extruded design.
The rear section of the previous sheet-and-tube design was composed of several sheet-metal parts that were welded and bolted together. To improve the adaptability of the cargo bed, Precicad separated the rear configuration into several parts. "The rear frame would still be composed of sheet metal parts but topped with a platform built with an extrusion. The extrusion would then allow us to custom build the platform to the needed dimensions in-house," explained La Chevrotiere. "Here again the extrusion is delivered pre-painted…cut to length and assembled together with 90-degree angles." This new platform, which is designed to accept an aluminum panel that is riveted in place, offers several options for the rear configuration, such as drop sides, closed boxes, tilting platform, tool box, and more. Channels in the extrusions allow incorporation of self-hardware to create mechanical bonding features.
![]() |
![]() |
![]() |
Honorable Mention: retrofit parking sign by Stephan La Chevrotiere of Service Precicad Inc
Stephan La Chevrotiere of Service Precicad Inc. also won an honorable mention for a retrofit parking sign for the City of Quebec. The city wanted a distinctive look for its parking signs that fit the environment of the old city, was discreet and met the standards of the UNESCO World Heritage site in which they were installed. The new design would have to fit over the existing posts and ease of installation was a major factor in the choice of the new design. Several other design criteria needed to be met, including integration of all information dictated by parking regulations, the ability to change information on the signs, anti-graffiti, and the inability for bicycles to be attached. The city also wanted the new design to be installed on the post in less than one minute. The final design that was chosen by the city was an extruded aluminum concept that completely covered the existing post.
The extruded design fit completely over the old post and was configured with a ribbed exterior making it harder to affix stickers. "The ribs also increase the rigidity of the structure without adding too much material," noted La Chevrotiere. In addition several interior ribs were included to guide the tightening device. "We also integrated a slide feature that allows the information panels to be easily installed or modified after initial installation," the designer explained. The spacing between the ribs was configured in such a way so that an information panel, also made of extruded aluminum, could slide easily in from the top on either side of the parking post. A cap, which is made of graphite with the ability to decorate with logos and identification, is then screwed on top to lock the extrusions in place and eliminate theft.
The City of Quebec installed 1,200 units throughout the city and feedback from installation crews showed that the simplicity of the system made the change to the new signs very easy. Maintenance is mitigated, according to the designer, since very little damage from graffiti and vandalism is occurring to the new parking posts because of the small discreet design.
![]() |
![]() |
![]() |
