
2005 International Aluminum Extrusion Design Competition
Professional Class Winning Entries
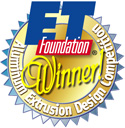
Grand Prize: Vertical Windmill, submitted by Randall Kearns
First Place Commercial/Industrial: Heatsink, submitted by Todd Kollar
First Place Structural/Consumer: CAJ Technology, submitted by Glenn A. Reynolds
First Place Structural/Consumer: Super Wonder Wedge, submitted by Jon Bricker
First Place Transportation: Retractacycle, submitted by John Dutton
Honorable Mention: KOBO process, submitted by Andrzej Korbel
Grand Prize: Vertical Windmill, submitted by Randall Kearns
![]() |
![]() |
The Grand Prize, awarded across all categories with a $5,000 cash prize, was presented to Randall Kearns, CAD Draftsman-Extruded Products at Hydro Aluminum North America in Ellenville, New York, for his extruded aluminum design of a vertical windmill.
Aluminum extrusion was used for the windmill concept because "it turns windmills into a simpler design and lowers cost for remote locations. It will withstand harsh environment and weather," explained Kearns. The windmill's vertical orientation resembles a tower with upright, elongated spinning blades able to catch the wind from any direction while producing 50 percent more power than conventional horizontal-mounted designs. The 100-foot model generates 5,000 kilowatts per hour in 12-mile-per-hour wind. The use of extruded aluminum makes the vertical windmill lightweight and quieter than conventional horizontal windmills and, therefore, more practical.
History reveals that the vertical windmill idea dates back hundreds of years.Providing a new twist on an old idea, the winning design maximizes its potential use by making it "an excellent concept utilizing aluminum extrusions that combines technology, creativity and potential marketplace application," according to Design Competition judge Dr. Joseph Benedyk, Contributing Editor for Light Metal Age magazine and Research Professor in the Mechanical, Materials & Aerospace Engineering Department of the Illinois Institute of Technology in Chicago. "This creative entry exhibited not only practicality and broad market potential but won high marks for sustainable development in addressing environmental and societal issues." This type of ground-breaking improvement "highlights the importance of the [Extrusion] Design Competition," Benedyk affirmed.
First Place Commercial/Industrial: Heatsink, submitted by Todd Kollar
First Place in the Professional Class for the Commercial/Industrial Category, with a $2,000 cash prize, was awarded to Todd Kollar, Sales Engineer for General Extrusions, Inc. (GEI) in Youngstown, Ohio, for a heatsink used in a touch-screen kiosk.
![]() |
![]() |
The winning aluminum extrusion heatsink design was the result of creating a customized, highly engineered part. "Our customer's original design incorporated standoffs that were to be inserted into milled holes located on the bottom of the heatsink," explains Kollar. "The locations of the standoffs were directly under the fins and/or hollow areas of the profile. In addition, the locations of the standoffs could not be altered due to mating components and assembly requirements."
To solve the problem, GEI came up with a unique solution: extrude the additional metal on the bottom of the heatsink where the standoffs were to be located and CNC (computer numerically controlled) machine the area to mill away the excess material to create the standoffs as built-in features of the extrusion itself. "GEI was able to use the extrusion process to create a more 'manufacturable,' less costly part without compromising the part's overall integrity with respect to the end use," Kollar stated. The judges were impressed with the complex shape of the part and GEI's solution to the standoff design problem. "Solving the problem by machining the base made this a winner," noted competition judge Angel Rosario, Applications Engineer for Alcoa Engineered Products in Chicago. "That's what extrusions are supposed to do."
First Place Structural/Consumer: CAJ Technology, submitted by Glenn A. Reynolds
The design applying Co-Axial Joint (CAJ) technology to antenna backup structures was one of two entries awarded First Place in the Professional Class for the Structural/Consumer Category, earning a $2,000 cash prize.
Glenn A. Reynolds of Gossamer Space Frames, Inc. in Long Beach, California, submitted the winning space frame design using 6061-T6 alloy. "This new structural joint design creates a rigid connection with the strength of a welded joint but without welding or bolting," Reynolds noted. V. Gary Curtis and Dean R. Hackbarth of Gossamer Space Frames, Inc. in Long Beach, California, along with Alfonso Feria and Asim Sehic of Jet Propulsion Laboratory, California Institute of Technology in Pasadena, California, helped Reynolds create the winning design.
The judges chose to award this entry because of its innovative technology and versatility of application across multiple markets. "Space antenna designs need to be very precise in order to maintain a viable signal," commented Design Competition judge Dr. Joe Benedyk, Contributing Editor for Light Metal Age magazine and Research Professor in the Mechanical, Materials & Aerospace Engineering Department of the Illinois Institute of Technology. "Traditionally, welding has been used to connect the joints, but welding can cause a variance in the antenna signal. This design solves that problem."
The CAJ connection is a non-welded, non-bolted mechanical attachment used to rigidly join multiple round tubular elements to a node in a structure. The components, consisting of three couplings, the block connector, and the tubular member, are all machine-threaded. The advantages of CAJ technology over other methods of joining pipes are many, including design, manufacturing, and field assembly. "In design, CAJ supports centerline geometries, increased strength-to-weight ratios, the use of different building materials—including weld-sensitive and exotic materials—and hollow connections for routing power conduit, communication and data lines, as well as cooling/heating air," Reynolds observed. In manufacturing, the components are easily machined in a standard CNC machine shop, part tolerances produced are inherently superior to conventional construction materials, and no welding is required. Field assembly advantages include hand tool assembly, ease of assembly in remote locations and quick assembly. The design translates across other markets as well, including a unique roller coaster-styled pedestrian bridge at the Pike amusement center in Long Beach, California, that employed the technology.
![]() |
The bridge is the first large-scale application of the CAJ technology, which offers economic, aesthetic, and practical advantages, according to the project construction manager. The economical advantage of the CAJ design was realized by the reported $500,000 savings. Aesthetically, the client, along with the City of Long Beach, desired a roller coaster design that offered maximum transparency, which the CAJ technology could deliver since field assembly procedures minimize difficult fitting conditions. The design itself resembles the Cyclone Racer roller coaster that was a popular attraction at the Pike from 1930 to 1968. Though the original roller coaster was made of wood, aluminum was the practical choice for the bridge to control the salt air's destructive nature. The 450-foot long, 87-foot high bridge is held together with 1,288 pieces of aluminum pipe connected with the patented CAJ requiring only one wrench and a few people to assemble, according to Reynolds.
First Place Structural/Consumer: Super Wonder Wedge, submitted by Jon Bricker
![]() |
![]() |
The Super Wonder Wedge design was one of two entries awarded First Place in the Professional Class for the Structural/Consumer Category, earning a $2,000 cash prize.
Jon Bricker, Industrial Designer and Manager of the Purdue University Exhibit Center in Lafayette, Indiana, created the winning Super Wonder Wedge design—an extruded aluminum joint construction device that is used to manufacture knock-down furniture. According to Bricker, the extrusion is designed to be sold in kits to accommodate different leg lengths, styles, and colors selected by the consumer. "The Super Wonder Wedge also allows for versatility and ease in assembly because it is a device that solidly assembles and locks together furniture without the use of either hand or power tools," explained Bricker. "We plan to use the Super Wonder Wedge in the fabrication of our knock-down exhibit furniture." Assembling and disassembling furniture using this hardware system will not cause damage.
Aluminum was specified because of high strength, light weight, and durability. The judges decided to recognize this entry in the Structural/Consumer Category because of its exceptional commercial viability.
First Place Transportation: Retractacycle, submitted by John Dutton
In an unusual turn of events, a student's design, the Retractacycle, outshined the entries submitted in the Transportation Category of the Professional Class and earned First Place with a $2,000 cash prize.
The Retractacycle retractable motorcycle seat designed by John Dutton, a sophomore majoring in industrial design at Purdue University in West Lafayette, Indiana, impressed the judges enough to elevate this winning entry from Student to Professional Class. Providing a real marketplace solution, the judges acknowledged the ingenuity worthy of the award. "This student's design is one that deserved to move up to this [Professional] level," commented Design Competition judge Angel L. Rosario, Applications Engineer for Alcoa Engineered Products in Chicago. "This is a great marketing idea offering a very practical application."
Initially, Dutton evaluated the motorcycle seats currently available on the market and then created an improved style based on its function and form. "Unlike the common dual seat found in front and back, this seat allows for the second rear seat to be folded up and stored away when not in use," Dutton explained. "The motorcycle seat consists of two aluminum extruded pieces of chosen color, one for each seat," Dutton continued. "The pieces are designed to slide in and out. The tubes on the sides…are designed to mimic the exhaust pipes running along the bike." The extruded pieces are then fitted with leather seat cushions. The back seat, when retracted, is pulled out with a rear handle and then clipped into two separately formed latches to hold it in place. In addition to convenience, the design provides cushion and color options that can be customized, adding function with aesthetic appeal. According to Dutton, extruded aluminum was used because the motorcycle seat "needs a strong support to sustain form."
Honorable Mention: KOBO process, submitted by Andrzej Korbel
Andrzej Korbel of the Department of Structure and Mechanics of Solids at AGH University of Science and Technology in Krakow, Poland, received an Honorable Mention in recognition for his work in developing ultrafine grained products extruded from aluminum and aluminum alloys. The KOBO process, as it is known, is a patented extrusion process that was developed by Korbel with Wlodzimierz Bochniak.
"The KOBO extrusion process provides the capability of extruding hard alloys at room temperature by creating friction at the die in order to produce fine grain products," explained Dr. Joseph Benedyk, Contributing Editor for Light Metal Age magazine and Research Professor in the Mechanical, Materials & Aerospace Engineering Department of the Illinois Institute of Technology. "The KOBO process is an emerging extrusion process with great potential for the industry. The process has been successfully applied to the extrusion of aluminum and copper alloys with the surprising results of extrusion force reductions of 40 percent and more," noted Benedyk. "This process could change the future of extrusion," commented Competition judge Bruce Kasten, Vice President of Sales and Marketing for Penn Aluminum in Murphysboro, Illinois.
The patented KOBO method is considered an unconventional method of metal forming that is able to produce ready-to-use products. "It is possible to use this [KOBO] procedure to obtain standard products from chips of metallic materials, which are a waste in the machining processes," according to Korbel and Bochniak. Other advantages include significant reduction of the deformation work (lower energy consumption), less wear of the tools, as well as elimination of annealing and etching between the particular operations (economical and ecological effects).
