
2012 International Aluminum Extrusion Design Competition
Professional Class Winning Entries
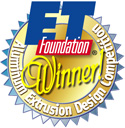
Grand Prize: Floor Panel Structure for Mercedes Benz SL by Harald Heinemann from Martinrea Honsel GmbH and Günther Johanntokrax from Mercedes Benz AG
Structural: Aluminum Lift Table by Rob Nelson from Almag Aluminum
Engineered Products: Street Signs for the City of Toronto by Shawn Comfort of Almag Aluminum
Renewable Materials: Aluminum Design Radiators by Dimitry Fotij of EMAX/VASCO
Cash awards and scholarships for the 2012 Aluminum Extrusion Design Competition sponsored by Hydro Aluminum North America, Inc.
*Click on the thumbnail of each image to be taken to the larger, higher-resolution image*
Grand Prize: Floor Panel Structure for Mercedes Benz SL by Harald Heinemann from Martinrea Honsel GmbH and Günther Johanntokrax from Mercedes Benz AG
The Grand Prize of $3,500, which was awarded across all completion classes and categories, went to Harald Heinemann of Martinrea Honsel GmbH and Günther Johanntokrax of Mercedes Benz AG of Germany for their floor panel structure for the aluminum body of the Mercedes Benz SL.
The Floor Panel Structure for the aluminum body Mercedes Benz SL automobile is made of three thin-walled aluminum extrusions using 80 percent recycled content. These are designed with a multiple-hollow structure to greatly reduce noise and vibration and form a dense barrier against water and fumes, offering substantial weight savings and superior stiffness. For the first time in an automotive application, friction stir welding is being used for a multiple hollow extrusion component. The 6106 T6 extrusions undergo sawing, CNC machining, friction stir welding, riveting, and passivation surface treatment. The ductile panel material increases energy absorption with high crushability and crack resistance. Extruded from complex dies, panels are machined and delivered with the required surface treatment.
"Mr. Heinemann and Mr. Johanntokrax have created a design which makes ideal use of the features and capabilities of aluminum extrusions combined with friction stir welding to create a strong, efficient, corrosion-resistant, lightweight structural automotive component" said competition judge Craig Werner. "The various elements of this extrusion design have been used previously, such as placing metal only where it is needed, creating near net shape solutions, leveraging the ease with which extrusions can be fabricated, and using friction stir welding to join together extrusions into wider assemblies, but the solution that they created pulls many of the elements together synergistically."
![]() |
![]() |
Structural: Aluminum Lift Table by Rob Nelson from Almag Aluminum
The winner of the Structural Category and a $2,000 prize was Rob Nelson of Almag Aluminum, Inc. in Brampton, Ontario, Canada, for his "Aluminum Lift Table".
The Aluminum Lift Table is used for patient transfer in the medical industry. The design uses two aluminum alloy 6063 side extrusions and one center extrusion, each fabricated with holes and customized with screw ports for end caps that are easily assembled into a 17" wide unit. The side sections are produced from one five-hollow extrusion with mirrored fabrication for right and left assembly. The center section is a three-port hollow fabricated to assemble with the sides. The lift table is lightweight, non-sparking, non-magnetic and strong, making it ideal for use around medical equipment. Screw ports are designed into the extrusion for securing end caps for final assembly. Using aluminum extrusion maintains a high strength-to-weight ratio, yet reduces the lift table's weight by 60 percent, from 220 pounds per unit down to 89 pounds per unit.
"Besides showing the obvious key structural and strength-to-weight advantages of the extrusion process, this medical lift is ideal for use in MRI machines because aluminum is not magnetic," Werner explained. "From a patient viewpoint, being able to be lifted and transported on this unit with less transfer onto other devices creates a more comfortable, secure environment during stressful times."
![]() |
Engineered Products: Street Signs for the City of Toronto by Shawn Comfort of Almag Aluminum
The winner of the Engineered Products category was Shawn Comfort, also from Almag Aluminum, for the streets signs currently being installed by the City of Toronto in Canada. He received a $2,000 cash prize.
The City of Toronto Street Signs utilize built-in slots and screw-ports to allow easy assembly. The efficient design eliminates multiple fasteners, reducing a 16 extrusion design down to just four extrusions, plus an end cap. Extruded aluminum alloy 6005A components are lightweight yet strong to withstand varying weather conditions. Extrusions are powder-coated or clear anodized, with a fabricated radius. The "neighborhood" plate slide fits into the top gap, which is finished to match the "municipal" address plate that slide fits into the bottom gap. Installation takes minutes by removing the end cap and sliding the blades for a cost-effective way to update without replacing the entire sign. Plates are easily changed in the field allowing unique neighborhood identity, yet retaining an overall consistent look throughout the city.
"What is remarkable about the street signage system developed by Mr. Comfort is the simplicity of design that he was able to develop in response to the need for new, corrosion resistant signage for the City of Toronto," commented Werner. "Earlier attempts by other designers resulted in more complex systems. Mr. Comfort's expertise with the extrusion process and design, coupled with his creativity, resulted in a signage solution that offers the use of corrosion-resistant aluminum extrusions, which is both easy to extrude and fabricate, painted and marked as desired. The signs can be repaired and ‘repurposed' for different signage needs with minimal effort or specialty tools."
![]() |
Renewable Energy: Aluminum Design Radiators by Dimitry Fotij of EMAX/VASCO
The winner of the Renewable Energy category was Dimitry Fotij of E-MAX/VASCO in Belgium.
The Aluminum Design Radiator series — Alu-Zen, Bryce, Canyon, and Zaros — features low energy consumption heat that is comfortable, safe, functional, and sustainable. The heater couples a convector's speed with panel radiator comfort, using low water volume and high-efficiency heat delivery. Aluminum alloy 6060 profiles are designed so that fins on the back provide convection and radiant heat is released in front, with hot water flow in the unit's core section. The aluminum design requires one-fifth of the water input, yet provides 15 percent more heat output than traditional radiators. Optimal output means the radiators may be used with low-temperature systems like heat pumps, further driving down home energy consumption.
![]() |
![]() |
