
2006 International Aluminum Extrusion Design Competition
Professional Class Winning Entries
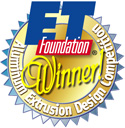
Grand Prize: Sea-Craft Rescue Bed (SEREBE)—Micah Bowers
Commercial/Industrial/Consumer: Multiroll Radius Sheet-Metal Hand Brake —Christopher Daniel Jeske
Structural: Totem Sit-Stand Leg—S. Ghosh, G. Varghese, and Venu Gopal
Transportation: Automatic Transmission Cooler—Al Howry and Larry Gillespie
Grand Prize: Sea-Craft Rescue Bed (SEREBE), submitted by Micah Bowers, industrial design student at Purdue University
For the first time in the history of the competition, the Grand Prize across all categories, with a cash prize of $4,000, was awarded to a student entry. Micah Bowers, a sophomore studying industrial design at Purdue University in West Lafayette, Indiana, won for his concept of a Sea-Craft Rescue Bed or SEREBE. The design employs the use of three extruded aluminum parts, is mounted onto a personal watercraft such as a Jet Ski, and is controlled by two electric motors powered by the watercraft's main motor. The three extruded parts consist of the outer extending arm, the inner extending arm, and the bed. "The inner arm has a track that allows rods to slide along it and unfold the third extrusion piece, [which] forms the foldable bed. due to a series of connecting hinges," explained Bowers in his entry materials. In use, the SEREBE serves as a litter to transport an injured person out of the water. "I'd take this to a manufacturer right away," commented competition judge Tom Ellis. "He's put a lot of thought into this; the hinge design uses the same extrusion that folds up for easy transport. This could have military applications." The SEREBE is the perfect application for water, since aluminum is noncorrosive and lightweight. Bowers used extruded aluminum in the design of the SEREBE "to ensure maximum strength and stability."
First Place Commercial/Industrial/Consumer: Multiroll Radius Sheet-Metal Hand Brake, submitted by Christopher Daniel Jeske, President of Rollfab, Inc.
First place winner in the Commercial/Industrial/Consumer category was Christopher Daniel Jeske, President of Rollfab, Inc. in Tampa, Florida, for the Multiroll radius sheet-metal hand brake. Jeske invented and developed the Multiroll after 25 years in sheet-metal education. Made of 6005 aluminum alloy, the product is currently in production, extruded by Almag Aluminum in Brampton, Ontario, an AEC member. "The machine has no moving parts and does not need electricity to run," according to the company's website. "You simply pull the metal over the die to form your desired degree on the one-inch radius die." Target markets for this product include architectural, custom automotive and motorcycle parts, arts and crafts," and whatever anyone else can dream of," stated Jeske. The extrusion caught the judge's attention due to the challenging offset void and difficult T-slot design. "If the die is not designed properly, the extrusion could cause a high degree of die breakage," commented competition judge Angel Rosario.
First Place Structural: Totem Sit-Stand Leg, submitted by S. Ghosh, G. Varghese, and Venu Gopal from Sudal Industries Ltd.
First place winners in the Structural category were S. Ghosh, G. Varghese, and Venu Gopal from Sudal Industries Ltd. in Maharashtra, India, for their design of the Totem Sit-Stand Leg, an extrusion used in office partitions. "This is an exceptional example due to the critical nature and shape of the profile with four screw bosses in one die mandrel, and half radius centre for assembly," noted the team from Sudal Industries. The judges agreed and awarded First Place to the design. The Sudal team submitted 12 entries for the 2006 Aluminum Extrusion Design Competition and the company has submitted multiple entries in each of the two previous Professional Aluminum Extrusion Design Competitions. "This goes to show that persistence does pay off," said Ellis.
First Place Transportation: Automatic Transmission Cooler, submitted by Al Howry and Larry Gillespie for Central Aluminum Company
First place winner in the Transportation Category was salesman Al Howry and engineer Larry Gillespie for Central Aluminum Company in Columbus, Ohio, an AEC member. The team won the award for their design of an automatic transmission cooler. The extrusion, made from 6063-T6 alloy, was the product of a brainstorming session with a local aftermarket automotive parts distributor. "We have done several parts for.Jegs of Delaware, Ohio. They were in a program to private-brand items for resale," the team noted in their entry materials. "In a brainstorming meeting . we looked at a heatsink shape we provide for another customer. They had been considering a transmission fluid cooler project. We traded sketches and a design was created for this part. The typical fluid heat exchanger is usually welded or brazed. Each seam is an opportunity for a leak. We took the heatsink, which normally allows for heat dissipation in the air and applied it to a fluid cooling application. We added lots of fins to aid in heat transfer. The shape is complex but easy to achieve with extrusion. The center fin is removed at one end to promote circulation."
The judges were impressed with the design. "It's got good symmetry; it's a complex extrusion," commented Ellis. "The extrusion replaces the welding assembly providing a no-leak feature," explained competition judge Joe Benedyk.
