
2004 International Aluminum Extrusion Design Competition
Professional Class Winning Entries
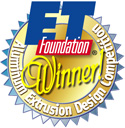
Grand Prize: Extruded roof rail for a Mercedes automobile
Architectural: Smartframe System
Commercial: New Wave Truss
Industrial: End cap (for uranium rod holder)
Residential: Sequoia Free Standing Lift System
Transportation: Suspension Link Rod
Grand Prize: Roof Rail, Submitted by Karl-Heinz Lindner, head of research and development for Erbslöh AG, Germany
The roof rail is a multivoid hollow shape made of 6060 alloy using a special rounding technique during the extrusion process. According to the judges, the unique rounding extrusion process developed by Erbslöh AG, along with the end product's glossy black finish and laser-marked Mercedes logo, made this roof rail exceptional not only within its category, but amongst all entries.
Using the rounding process during extrusion to create the lightweight automotive space frame component maximized the formability of the aluminum, thereby offering uniform, even surface topography that avoids the pitfalls of an orange-peel surface or grooves created by previous cold-working methods. The roof rail was extruded to extremely tight tolerances making it suitable for laser welding. Aluminum alloy was the material of choice to minimize weight, which is crucial to reducing fuel consumption, a critical concern in the automotive market.
First Place Architectural: Smartframe, Submitted by Wyatt Frantom, Adam Janusz, Joe Meppelink, and Onezieme Mouton at FrameWork of Houston, Texas
Zeroing in on the growing need for low-cost housing, the architects designed the Smartframe© System, a simplified, easily-assembled house framing system, to deliver affordable, mass-producible, quality housing using a multi-cellular extruded aluminum assembly that carries cold air, hot and cold water, electrical, and data utilities all within its profiles. The Smartframe home "kit" system is a modern-day erector set, featuring five continuous extruded aluminum cross-sections, combined with rectangular tube sections to create a flexible and easily assembled frame. FrameWork architectural designers Adam Janusz, Joe Meppelink, Onezieme Mouton, and Wyatt Frantom's vision goes beyond the scope of traditional building-and-construction uses for extruded aluminum windows and accessories. The architects were inspired by extruded aluminum framed canopy systems and structural systems for sunrooms, which prompted them to ask, "Why not an entire house?"
First Place Commercial: New Wave Truss, Submitted by Peter Hind, Vice President of Engineering at Total Structures, Inc., Ventura, California
Chosen for its excellent functionality and features, the winning design innovation uses complex extruded web sections of 6005-T5 alloy to form the A-wave series of the New Wave Truss line, making it capable of generating a multitude of design options. Anodizing produces a range of colors and textures that goes beyond the typical polished silver and powder-coated finishes.
Offering appealing alternatives to the traditional aluminum trusses, this versatile design presents aesthetic qualities in chords and structures never seen before. Designers at Total Structures teamed up with an original-equipment composite manufacturer to develop an aesthetically pleasing truss structure with less distortion during extrusion and the ability to slice extrusions to form structural shear webs. Truss diagonals cut on an angle, and perpendicular end frames are formed from an extruded plate. The complex extrusion is economical to produce and can also be cut using electrical discharge machining (EDM) to incorporate logos directly into the truss.
First Place Industrial: End Cap (for uranium rod holder), Submitted by Sankarlal Ghosh, Vice President of Operations at Sudal Industries
Given its ability to achieve complex shape requirements and meet demanding tolerances, extruded aluminum was the material of choice for the end cap that is used with a uranium rod holder found inside nuclear reactors. According to the competition judges, "extruding 5052 alloy into such a complex shape for such an exotic application" made the end cap outstanding in its category. By using aluminum extrusion, rather than the previous low-pressure die casting method, this essential part can be produced with high dimensional accuracy at a drastically reduced cost, offering higher productivity, sound mechanical strength, porosity and shrinkage-free recovery, and no machining required for a smooth surface finish.
Reliability and structural integrity are always of critical importance in nuclear power equipment. The extruded aluminum end cap, consisting of a six-void hollow shape with good weld seam quality, has a vital function in keeping the uranium rod holders safe in a potentially volatile environment. According to Ghosh's submission details, the 5052 alloy was specifically chosen in producing the end cap for its non-heat treatable qualities as required for its end use.
First Place Residential: Sequoia Freestanding Lift System, Submitted by Joe Jackman at Almag Aluminum, Inc., Brampton; and Mark Chepurny and Mikel Shani at Waverley Glen Systems, Ltd., Concord, Ontario, Canada
The adjustable freestanding extruded aluminum Sequoia lift is designed for home health care and constructed in a manner that requires only one person and no tools to assemble. The Sequoia significantly improves mobility for the user while offering design advantages of strength and versatility. Using 6005 aluminum alloy allowed for the strength (yield and tensile) needed to create the unit. The lift is lightweight and portable, yet strong enough to support 400 pounds. It can be carried by one person and fits inside the average car making it convenient to use for activities such as traveling and camping. The Sequoia also saves the prohibitive expense of purchasing and installing a permanently mounted lift system in the home.
"The low cost of the aluminum extrusion process has also been beneficial," stated Waverley Glen senior designer Mark Chepurny. "There are several components on our system that could have been permanent mold cast; we opted for the extrusion process because it not only allowed us to produce the final parts at a lower cost, the tooling prices were also much lower."
The designers devised the system using 13 different aluminum extruded profiles, totaling 31 parts. Designers pushed the extrusion envelope by addressing more than 40 points of contact over two key profiles: the system's top and bottom tracks. The strong, lightweight tracks are constructed and manufactured to tight tolerances to allow the trolley to run seamlessly between each profile and maximize system stability. Twist, straightness, and bow on both profiles are extremely tight, so that one profile slides inside the other over a 66-inch length, allowing profiles to easily span up to nine feet. Chepurny notes, "We required the track and support posts to be telescopically adjustable, and without the precision and strength of the aluminum extrusion process, this would not have been achievable." Beyond its structural integrity, the clear satin anodizing gives it an appealing finish.
First Place Transportation: Suspension Link, Submitted by John Vanderzyde of Kaiser Aluminum in Ontario, Canada; the part was manufactured for Tower Automotive.
After Tower designer engineers evaluated different materials and processes, aluminum extrusion prevailed as the material of choice because it satisfied the objectives for designing a stronger, lighter weight and less costly component with improved suspension performance over its steel tubular predecessor. The suspension link rod was extruded using a 6061-T6 multivoid hollow design coupled with friction stir welding and consisting of a two-piece component with a single weld. The resulting suspension link was 27 percent lighter than the previous steel design with equivalent or improved suspension performance, higher tensile strength, higher fatigue testing, and ultimately a more cost-effective suspension system. Added benefits inherent in using aluminum extrusion included a high strength-to-weight ratio, corrosion resistance, low tooling costs, and the ability to produce complex shapes and meet demanding tolerances.
Currently in production on the Lincoln Town Car, the winning design represents an innovative application for aluminum extrusion. Referring to the suspension link in his submission details, Vanderzyde noted, "Its success is an integral reason why designers continue to evaluate the use of aluminum extrusions for the structural components of automobiles. Aluminum extrusions time and again prove to be the material and process of choice over steel where weight, strength, manufacturability, and costs are important design parameters to the designer."
